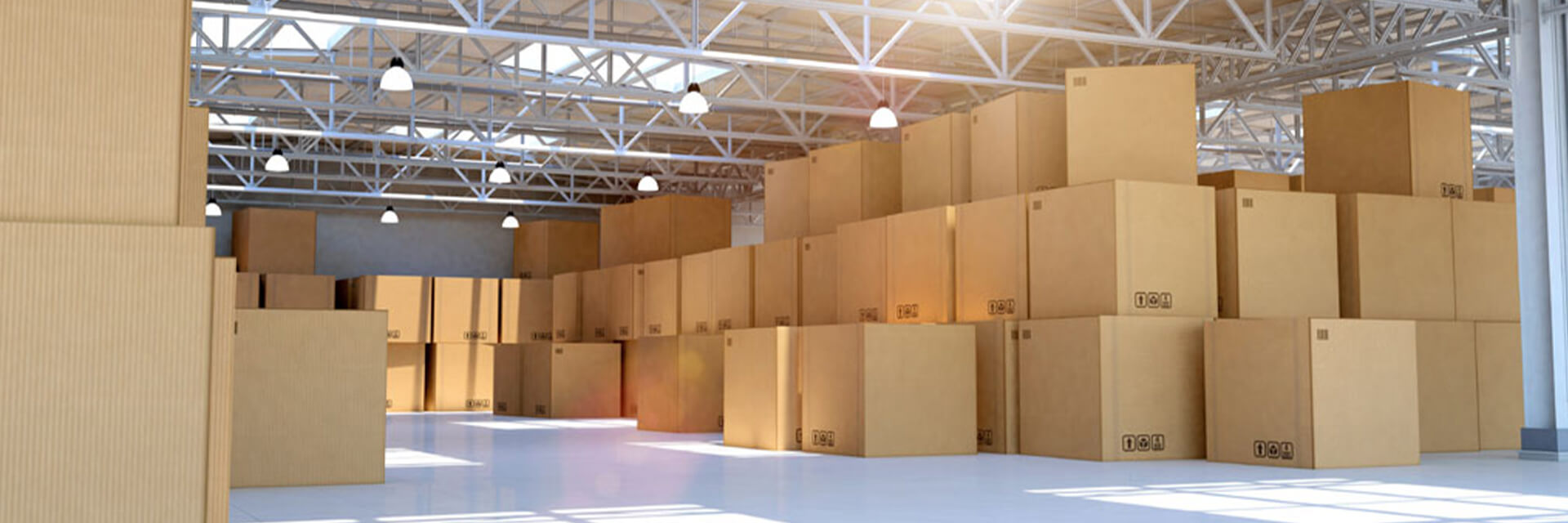
Where Have All the Manufacturing Workers Gone?
- Published
- Mar 1, 2022
- Share
The lack of skilled labor is deemed the greatest threat to the U.S. manufacturing industry, according to the Center Directors for the National Manufacturing Extension Partnership program.
This is not a new issue and was flagged by the Information Technology and Innovation Foundation almost ten years ago as a major factor impacting the global competitiveness of U.S. manufacturing. And now, COVID-19, along with a myriad of immigration policies over the past several years, seems to have exacerbated the issue. A small manufacturer in New Hampshire recently bought a patent that would allow him to quickly expand his product offering and market. He already has inquiries from around the world wanting to purchase the product for which he now holds the patent. However, the manufacturer can’t build his product because he can’t find skilled workers to fill the positions necessary to meet the market demand.
Why is this happening? It is a combination of factors. Baby boomers are retiring, leaving skill gaps in their wake. Millennials, now moving into middle age, steered clear of manufacturing as they came of working age during the Great Recession, fearing a lack of job stability when many manufacturers were not hiring. In addition, they, and the rising Gen Z, were often misled or misinformed about the nature and value of manufacturing careers. Thus, they tended to opt for other jobs that seemed less “dirty” and “physically demanding.” This is the great myth of manufacturing. Many of the jobs available today are highly technical and advanced, requiring engineering, project management and problem-solving skills under the roofs of shining facilities with technical advancements to rival Star Wars. Manufacturing can offer a long and stable career with excellent pay, opportunities for advancement and professional development.
What can manufacturers do to attract and retain workers? Discussions with many of our clients and strategic partners in the manufacturing sector have shown that there are some solutions that seem to be gaining traction.
Short-Term Solutions
Create a Clear Path of Progression – Help prospective employees understand what a career in your company might look like from the first few months of training and onboarding through certification, position advancement, management and leadership opportunities. Demonstrate how dynamic and exciting this field can be, and ensure that your company representatives know how to paint a picture of long-term development and success.
Offer Flexibility – Many employers today have found ways to shorten working hours by hiring more part-time employees or offering job-share opportunities. Research indicates, and many employers will attest, that younger generations are seeking a more balanced approach to their work and personal lives and are thus more likely to join companies that can offer a more flexible and family-friendly schedule.
Speed the Availability of Wage Access – Money talks, and while a business may not be able to increase wages, it may be possible to move from bimonthly to weekly paychecks and make access to one’s wages easier.
Pay Performance Bonuses Regularly – Gone are the days when just an annual bonus will suffice. Workers want to know when they are doing a good job and be rewarded for their efforts. This might be in the form of cash or other benefits. One company offered the use of the owner’s impressive lake house for a long weekend for outstanding employees who exceeded performance targets. The critical part is to link the bonus directly to agreed performance metrics and offer it in a timely fashion.
Involve Employees in Programs That Benefit More Than Just the Company – Younger workers have expressed a strong interest in working with a purpose, knowing that somehow their efforts will make a difference in the world or in the lives of end users. This may include becoming involved in company charity efforts or community-supported programs that impact the greater good and can help fulfill the desire to work for more than just a paycheck. There are many companies today that offer software to support, encourage and track employee volunteer activity as well as offer incentives and opportunities to connect with others in the organization with the same charitable interests.
Pre-Employment Paid Time Off (“PTO”) – Some businesses now offer new employees the opportunity to take PTO before they start their new jobs. A week of PTO might be pretty enticing to someone entering the workforce right after college or switching from a demanding job.
Sign-On Bonuses – While sign-on bonuses have been around for a long time, more companies are offering larger bonuses or offering to pay all or some of a new employee’s college loans over time. Money speaks, and for many young workers struggling under a mountain of debt, a sign-on bonus can be especially attractive.
Long-Term Solutions
Invest in Your Training Force – Many manufacturing jobs require licensing and certification, a process that can last several months to several years with many tests along the way. To keep workers motivated and engaged, they need to work with skilled on-the-job trainers who know how to teach, inspire, lead and coach their protégés to be successful. Too many young workers leave the field because they find the process of becoming certified, often the only way to earn better wages, to be burdensome, too long and frustrating. Investing in great trainers, rather than delegating the task to a senior team member, and providing them with the resources they need to be better educators can pay big dividends over the long term.
Partner with Local Programs – Provide education and opportunities at a young age (Boys and Girls Clubs, 4-H, YWCA, Boy Scouts and Girl Scouts, high schools, middle schools). Ensure that young people can learn more about the current benefits and exciting future of manufacturing and how they can get involved. Consider sponsoring local science, technology, engineering and math (“STEM”) programs.
Tell the Story – Encourage young people in the field to share their experiences via social media, school visits and events.
Work with Local and Regional Policy Makers – Fund and reinstitute technical programs that operate seamlessly from middle school through college, and consider working with local, regional and national policy makers to enact sensible immigration programs that provide skills training to committed individuals who want to make a new life in a new country.
The labor shortage across the country isn’t going to change quickly, and we’ll need both long- and short-term solutions. However, there are still many reasons to be optimistic. New advances in manufacturing technology, such as 3D printing, are finding a new audience in younger generations. It looks like fun because it is! Manufacturing offers the opportunity to work on the cutting edge of innovation, and more people are beginning to see the possibilities.
STEM programs are being developed and offered across the globe, attracting more women and disadvantaged youth, and this can only be good for manufacturing. Many predict a coming manufacturing renaissance as more people realize that developing our products locally, with advanced technology, leads to a stronger economy, stable communities and a happier, more productive workforce.
Contact EisnerAmper
If you have any questions, we'd like to hear from you.
Receive the latest business insights, analysis, and perspectives from EisnerAmper professionals.